
Boost Wire Output with These Expert Tips for Operating Water Tank Drawing Machines
Category:Blog
Author:
Source:
Add time:2025-06-30 10:46
Tired of your Water Tank Wire Drawing Machine running below its potential? You invested for high output – yet bottlenecks keep dragging down production. Good news: Small operational tweaks deliver big gains. Here’s how expert operators squeeze 20%+ more wire from machines like the DLW-350 – without buying new equipment.
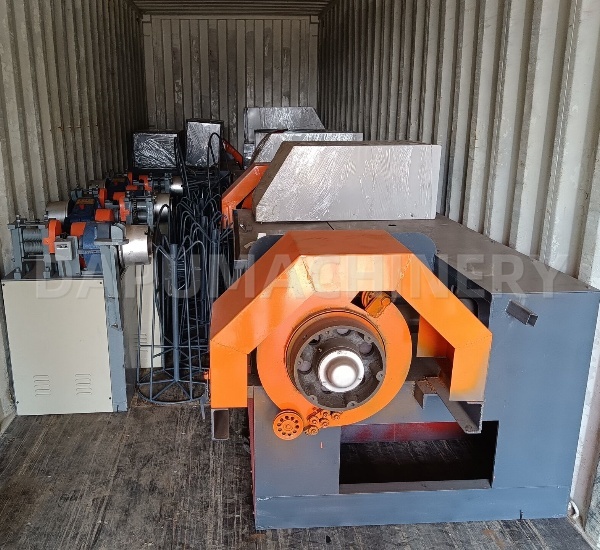
1. Master Coolant Control: The Secret to Speed & Quality
Problem: Dirty or hot coolant causes wire breaks and forces speed reductions.
Expert Fix:
Temperature: Keep coolant below 30°C (use a chiller if needed). Why? Prevents overheating at 700 m/min.
Cleanliness: Filter daily. Change coolant monthly. Why? Grit scratches wire and wears CD molds faster.
Concentration: Follow supplier specs. Why? Wrong mix = poor lubrication → breaks.
Result: Run at max speed (700 m/min) consistently with <0.5% breakage.
2. Optimize Die Setup & Maintenance
Problem: Misaligned or worn dies create uneven wire, scraps, and downtime.
Expert Fix:
Sequence Check: Verify die order matches your reduction (e.g., 2.2mm → 0.6mm sequence).
Alignment: Use laser guides. Why? Even 0.1mm misalignment strains wire.
CD Mold Care: Clean dies with ultrasonic baths weekly. Never use abrasive tools!
Result: Smoother wire, +15% die life, fewer emergency stops.
3. Maximize Coiling Efficiency (Stop Wasting Time!)
Problem: Frequent coil changes kill momentum – especially with small spools.
Expert Fix (DLW-350 Focused):
Fill to 95%: Use the full 350 mm trunk coil capacity – don’t underload.
Tension Settings: Adjust for wire thickness. Thin wire (0.6mm)? Lower tension to avoid snaps.
Automate Changeovers: Add a transfer cart for 60-second swaps.
Result: Gain 1+ extra production hours per shift by minimizing stops.
4. Track & Tweak These 3 Performance Metrics
Stop guessing – measure what matters:
Uptime %: Target >92%. Track stops >2 minutes (coil changes, breaks, jams).
Meters/Kilowatt Hour: Monitor your 30 kW motor efficiency. Drop = check bearings/dies.
Scrap Rate: Aim for <0.8%. Spikes signal coolant/die issues.
Pro Tip: Log speed per pass. If you can’t sustain 700 m/min on later dies, check die wear or coolant flow.
5. Pro Operator Upgrades (Low Cost, High Impact)
Pre-Heat Treatment: Anneal wire before drawing tough alloys. Cuts drawing force by 20%.
Variable Speed Zones: Slow down entry dies (2.2mm), max out later stages (0.8-0.6mm). Reduces breaks on fine wire.
Vibration Sensors: Mount on frame (1900 KG machines still vibrate!). Catch bearing failures early.
DLW-350 Optimization Cheat Sheet
Goal | Setting/Check | Target |
---|---|---|
Max Speed | Coolant temp + die alignment | Sustain 700 m/min |
Reduce Scrap | Coolant pH (7.5-8.5) + tension settings | <0.8% scrap rate |
Extend Die Life | Ultrasonic cleaning + reduction per pass | CD molds last 8+ months |
Minimize Stops | Coil fill level + auto-transfer system | <4 coil changes/shift |
Unlock Your Machine’s True Potential
Your Water Tank Wire Drawing Machine is built for speed and precision (like the DLW-350’s 700 m/min and 0.6mm capability). But operators hold the key to max output. Implement these tips to:
Produce 20%+ more wire per shift
Slash scrap costs
Avoid unplanned downtime
*“A well-tuned DLW-350 outperforms a cheap machine running ‘full speed’ by 40% in real output – thanks to less stopping and waste.”* – Plant Manager, Steel Cable Co.
Ready to blast past limits? Start with coolant and coil management today. Track your metrics for 1 week – you’ll see the difference.
Recommend News