
Water Tank vs. Dry Wire Drawing Machines: Which One Should You Choose in 2025?
Category:Blog
Author:
Source:
Add time:2025-06-30 10:50
Choosing the right wire drawing machine impacts your productivity, costs, and product quality. While dry machines are common, Water Tank Wire Drawing Machines are transforming modern production. Here’s a clear comparison to help you decide:
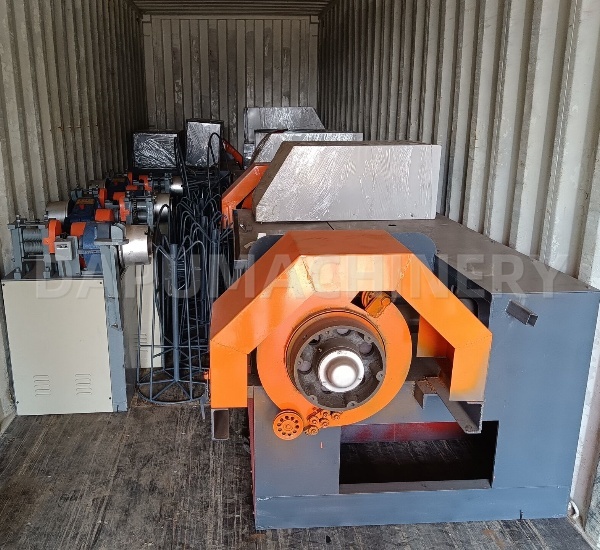
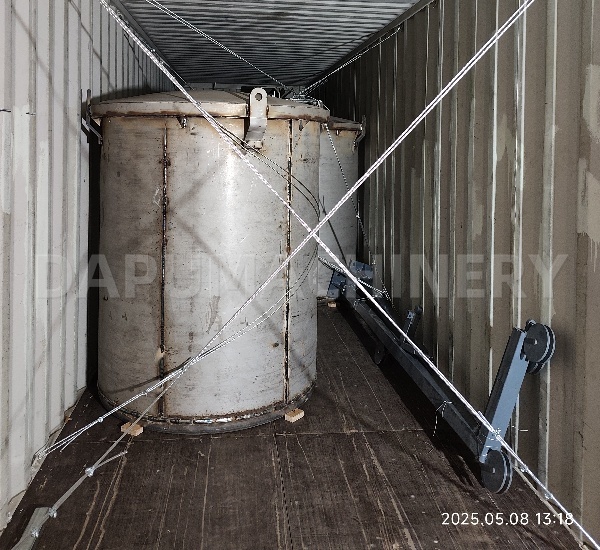
Key Differences at a Glance
Feature | Water Tank Wire Drawing Machine | Dry Wire Drawing Machine |
---|---|---|
Cooling Method | Wire/dies fully immersed in coolant | Air-cooled or minimal lubrication |
Wire Quality | Superior surface finish, no overheating | Risk of oxidation, surface defects |
Production Speed | Sustains 700 m/min (e.g., DLW-350) | Slows down to prevent overheating |
Die Longevity | CD molds last longer with cooling | Dies wear faster due to friction |
Noise/Dust | Low noise, no airborne dust | Loud, generates metal dust |
When to Choose a WATER TANK Machine
You Demand Flawless Quality
Ideal for: Medical wires, electronics, aerospace cables.
Why: Water cooling prevents surface cracks and ensures precise sizing (e.g., 0.6 mm±0.01 mm on DLW-350).
You Need High-Speed Production
Ideal for: High-volume orders, tight deadlines.
Why: Stable cooling allows continuous 700 m/min operation without quality loss.
You Use Hard Materials (e.g., Steel, Alloys)
Ideal for: Springs, tire cords, industrial cables.
Why: Water reduces friction, enabling smooth reduction from 2.2 mm to 0.6 mm.
When a DRY Machine Might Suffice
Low-Volume, Simple Wire Production
Example: Thick fence wires (>3 mm), non-critical applications.
Caution: Speeds rarely exceed 300 m/min.
Minimal Maintenance Needs
Advantage: No coolant tanks to clean.
Trade-off: Frequent die changes increase downtime.
Tight Initial Budget
Reality: Dry machines cost 20-30% less upfront.
Long-term: Higher scrap rates + energy costs reduce savings.
The Hidden Costs of "Saving Money"
Cost Factor | Water Tank Machine | Dry Machine |
---|---|---|
Wire Breakage | <1% (cooling reduces snaps) | 3-5% (overheating weakens wire) |
Die Replacement | Every 6-8 months (CD molds) | Monthly (high friction) |
Energy Use | Optimized (30 kW motor) | Overworked motors at high speeds |
Why Most Manufacturers Choose Water Tanks in 2025
*"A DLW-350 Water Tank Machine produces 3x more wire per shift vs. a dry machine at the same speed – thanks to zero downtime for cooling breaks."*
Key Advantages:
Zero Overheating: Water maintains consistent wire temperature.
Perfect Surface Finish: Essential for plating or coating.
Maximized Uptime: Large 350 mm trunk coils + durable dies = fewer stops.
Future-Proof: Handles ultra-fine wires (down to 0.6 mm) at industrial speeds.
The Verdict
Choose a DRY machine if:
You produce thick, non-critical wires occasionally.
Budget constraints outweigh long-term efficiency.
Choose a WATER TANK machine (like DLW-350) if:
Quality is non-negotiable (e.g., automotive, aerospace).
You run high-volume shifts and need 700 m/min reliably.
Reducing scrap and downtime is critical.
Pro Tip: Hybrid machines exist, but dedicated water tanks (e.g., DLW-350) dominate precision wire production. Their heavy frame (1900 KG) ensures vibration-free operation – dry machines can’t match this stability.
Upgrade Smartly in 2025
For 90% of industrial wire drawers, Water Tank Wire Drawing Machines deliver lower cost-per-meter and premium quality. Calculate your ROI: Faster speeds (700 m/min) + near-zero scrap + fewer die changes (CD molds) = profit growth. Ready to leave dry machines behind? Explore how the DLW-350 can elevate your production.
Recommend News